
Often, the initial causes you identify are actually symptomatic or a secondary cause of a deeper issue. These causes can be listed in your diagram by connecting them to the “bone” of the factor they fall under. For an Equipment or Machine category, you may identify an equipment failure. For a Manpower or People category, you may identify that an employee skipped a step or that there was no manager available to approve the product at a certain step in the process. Next, brainstorm specific causes that may occur or identify things that occurred within each of the categories your team defined. Step 3: Brainstorm Specific Causes Within Each Factor These categories become the “bones” of your fishbone diagram.
#Ishikawa diagram machine vs material free#
Feel free to edit the categories as needed for your business, but be careful not to exclude anything that may have contributed to your issue.

Depending on the situation you’re investigating or your business model, these categories may fit perfectly or they may not resonate. Some teams use “the 6 Ms” as these categories: Manpower, Material, Method, Mother Nature, Machine, and Measurement. These should be broad categories to guide brainstorming, such as Equipment, Environment, Rules/Procedures, and Staff/People. Second, consider what types of factors could have contributed to the problem. Step 2: Identify the Potential Factors Causing the Problem
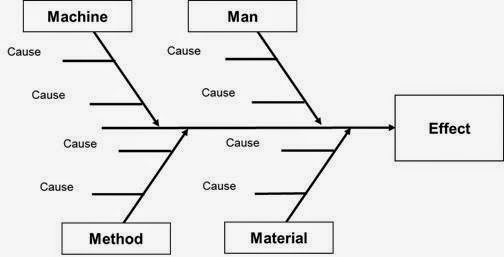
#Ishikawa diagram machine vs material how to#
Get started with a free trial of Gliffy to make your own fishbone diagram > How to Use an Ishikawa Diagram for Root Cause Analysis What is Root Cause Analysis? Manufacturers need to ensure that their output is consistent and predictable, so understanding what could cause variation will help them create better processes. By considering what can go wrong, designers can strengthen each step or adjust the process to be as efficient and reliable as possible.īecause fishbone diagrams work by identifying possible issues and failures, they’re especially valuable in fields like supply chain management and manufacturing. Brainstorming everything that could cause a process to fail helps process owners manage existing processes, but can be even more effective while designing a new process. Want to get started right away? Make an Ishikawa diagram with a free trial of Gliffy Online > What is a Fishbone Diagram Used For?įishbone diagrams work by helping process designers brainstorm the potential causes for a particular problem.
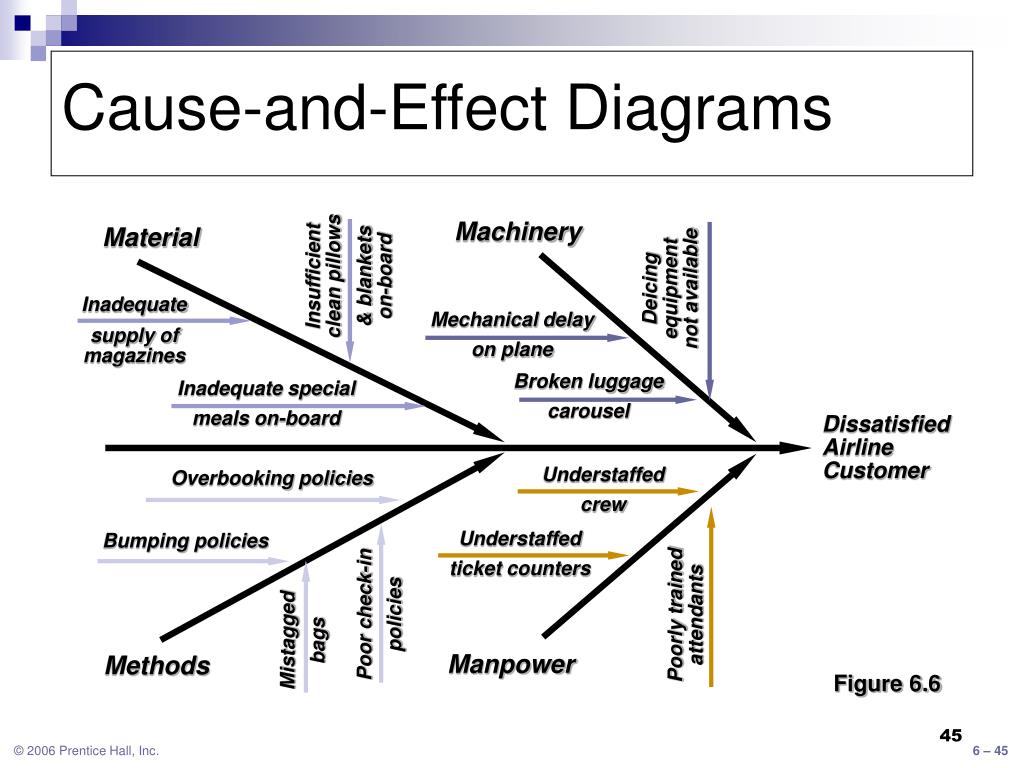
